ASA Emulsifiers
Amplified Turbine Shear (ATS)
The NORCHEM ASA emulsifiers use a combination of a proprietary emulsifier pre-conditioning manifold, low volume recycle loop and high-speed turbine rotors to create an emulsion with the proper particle size and distribution to improve sizing response. Unlike conventional ASA emulsifiers, which are normally limited to two adjustments, (recycle rate and turbine pressure), the NORCHEM systems add a third proprietary dimension, adjustable turbine shear events. This patented feature found exclusively on NORCHEM ASA emulsifier systems, improves the emulsion particle size and narrows the overall emulsion distribution characteristics to promote better sizing response, enhance emulsion stability, and reduce dosage requirements.
The ability to adjust particle size and distribution through the emulsifier loop can be illustrated by using these particle analyzer graphs. A baseline operating condition is established through the emulsifier and a particle size test is run. The adjusted parameters (independently controlled) are ASA to emulsifier ratio, primary turbine flow, turbine pressure, recycle pressure, turbine inlet pressure and turbine rotor speed (expressed in Hz). The emulsion sample is evaluated for overall mean particle diameter and particle size distribution. (standard deviation)
First Sample Run
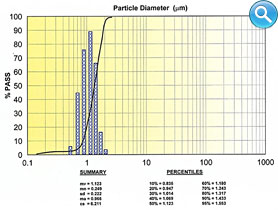
The initial run through the emulsifier produced an emulsion with a 1.1 micron median particle size. To improve sizing response and lower the dosage demand, optimization to the emulsifier was initiated.
Emulsifier Model: | NORCHEM AP2000 VS |
---|---|
ASA Flow rate: | 1100 ML/MIN |
ASA to Emulsifier ratio: | 1:0.66 |
Overall mean diameter: | 1.123� |
Particle range: | 10% = 0.825� |
95% = | 1.55� |
Over 2.0�: | 0.71% |
Standard deviation: | 0.222 |
Second Sample Run
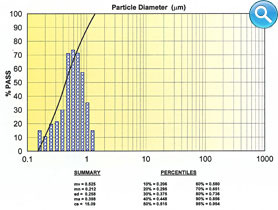
To reduce the particle size of the emulsion, an increase in ATS (amplified turbine shear) was applied to produce a significantly smaller particle. A subsequent distribution shift into the sub-micron range evolved.
Emulsifier Model: | NORCHEM AP2000 VS |
---|---|
ASA Flow rate: | 1100 ML/MIN |
ASA to Emulsifier ratio: | 1:0.66 |
Overall mean diameter: | 0.525� |
Particle range: | 10% = 0.206� |
95% = | 0.954� |
Over 2.0�: | 0.00% |
Standard deviation: | 0.258 |
Third Sample Run
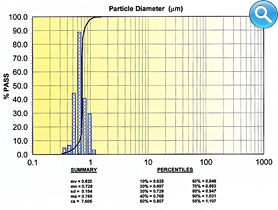
To restore the distribution profile, a minor adjustment to the emulsifier manifold block operating parameters resulted in an improved standard deviation, resulting in an improved emulsion quality.
Emulsifier Model: | NORCHEM AP2000 VS |
---|---|
ASA Flow rate: | 1100 ML/MIN |
ASA to Emulsifier ratio: | 1:0.66 |
Overall mean diameter: | 0.820� |
Particle range: | 10% = 0.625� |
95% = | 1.107� |
Over 2.0�: | 0.00% |
Standard deviation: | 0.154 |
In this instance, the overall improvement to the emulsion quality is in the particle size and uniformity. (compare the standard deviation values among the three samples) While the first sample is a good emulsion in terms of particle size and distribution, the second and third samples are better emulsions with regard to sizing response. In the actual sizing application using the optimized emulsion, the paper machine production rate improved in a predictable manner without the penalty of higher chemical costs associated with increased dosages.